Profile of a Master Bladesmith
A personal history...
Artist Profile
Hi, my name is Jerry Fisk; I have been living and working full-time as a Master Bladesmith since 1989. I received the honor of being named a National Living Treasure in 1999. Please see the Awards link for a complete history of where I have been and what I have done. And, yes, I did wear clean underwear along the way as my mother taught me.
Most of my pieces are created using natural materials for handles. The blade steels I prefer are traditional carbon steels or I will blend various steels to make my own Damascus.
I continue to push myself to improve what I do know and to learn new skills and techniques so that I can offer you the best work that I can currently do. I prefer to engrave the pieces that I make as I think it makes the package complete though the piece must stand on its own merits without ornamentation.
All of my blades from field grade to ornate pieces are tested to insure they perform in the manner for which they are designed for and made as strong as the design allows.
In these modern times you have to search for something that a craftsman/artist makes one-at-a-time. The days of one person working in their shop to create functional works of art are fast going, as it seems we live in a disposable world. This is your time to own something for you and your family that can be passed down. Each generation will have its own stories of the piece and the memories it holds for them. That is something to treasure for the ages.
Let me give you a bit of personal background information about myself...
I was one of five boys in the family. We grew up without much. Dad bought an old, abandoned house for $250, if I remember right. When it rained, the roof leaked. Each of us boys had to watch his own spot for leaks and not let the pans or buckets overflow on the floor.If the floor got wet, mom tanned our hides.When it was time for a bath, I toted buckets of water into the kitchen for the tub. Until I was 10 years old.I thought my name was "boy, go get water". I was about 15 when we finally got running water in the house and an indoor bathroom. By then, it almost seemed wrong to go to the bathroom inside the place you lived.
I got to watch an old blacksmith make dad's cattle brand when I was 10. After it was made, he heated it up and branded the wall of his shop along with all the area's other brands. Then he discovered he put the "f" in backwards, so I watched him take it apart and do it right. He sure made the sparks fly when it was red hot. I wanted to try that, but he wouldn't let me. Of course, back then I wanted to try lots of things I had no business doing. (I'm not much different now.)
Another old Blacksmith moved into our area when I was 11. He came to town without much money, so dad, a preacher, helped him set up his shop. After church, mom and dad would let me stop by to look at his knives when he set up on side of the road with a fold up table to display his knives. Those were the first forged blades I ever saw. When I was in sixth grade, my class took a field trip to the old Washington Blacksmith shop where James Black forged a knife for Jim Bowie. This was pretty close to the same time frame. Now I had to try it for sure.
Because of the way that I was raised, a knife to me is first a tool, and second it is pretty to look at, if done right. This is just the way I was raised. Work hard and use a good tool.
Why I make knives...
I make knives and edged tools because of a life-long interest and desire. The only limits to this field are those I put on myself. Lots of times I blend centuries-old techniques with modern methods. I prefer designs drawn from something that simulates nature and prefer to work in natural materials.
Forging knives for a living has been a hot and dirty job throughout history. It is no different now. The glamour fades quickly as you burn the shirts off your body.
When I was asked once, why I make knives, I said, "...to show that I lived". My work will last hundreds of years longer than I will. But now they will know I was here."
I would like to talk to you a bit about the construction and design of my knives...

I use both one piece handles and mortised tang handles for my concealed tang knives. Many times the mortised handle is better on natural materials. Natural materials has a tendency to move with the weather or as they dry out. Having the handle mortised allows the handle material a natural fault line so that it moves instead of cracking. When I mortise the handle, I cut the handle materials so that there is only a maximum total of .004 inch between the handle material and the tang thickness of the knife. This allows a good fit with a bare minimum of bonding materials. Tang length on all of my knives without pommels range from within 1/2 inch to 1/8 inch of the back of the handle [depending upon design of the knife]. This insures the handle and tang will hold up under tremendous abuse.
A knife with a straight handle gives more speed!
A handle that has drop in it has more power. The more you drop it down the more power it has but the less speed. So you have to balance what you want the knife to be used for with the actual design. There is no perfect knife to all chores.
If the desired knife gets a temper line I can make them straight [standard] or use the clay coating method and give it a nice wavy line of some sort. Then the knife can be etched and polished with automotive polishing compounds using leather as a backing for the compounds. This will give a gray type finish on the blade that actually helps retard the rust and looks really nice. This type of treatment and polishing costs a bit more due to the more time involved.
I make my knives as strong as I possibly can!
Even if you say you will never use the knife. I believe in making the knife right and as good as I can possibly make it at the time. I will continue to push and learn more about how to make you a good knife.
I press fit my guards on the blades
The guards can come in many different materials on your knife. German silver, steel, stainless steel, damascus, bronze, copper and wrought iron. You can do several things with some of these, for instance steel guards can be left as is, or they can be blued or browned. One of my favorites is wrought iron. I have a small supply of pre civil war wrought iron. To work it for instance it has to be forged to shape, then ground, then mirror polished and at that time I put it in muratic acid for about a 60 second etch to bring out the natural grain flow of the iron. This looks really nice.
Fluting my handles
I hope you like some of my fluting. One of my favorites to look at is the gain twist fluting, [see Hope's Unicorn] along with being my favorite to look at it is also the one that gives me the most terror and the most hand cramps. There are two types of fluting. Convex and Concave. Concave is easier to do and does not take near as much time. I prefer to see the convex. The only way to do this is to sit down with a three cornor file. This takes a lot of time. Once you have it layed out, and that is another reason you do not see very little gain twist, the lay out is a booger. Once filed then you take and glue sandpaper to ice cream sticks to clean those lines up. At that time I use fine steel wool to get it closer to polished. Then finer sand paper and finer till you got it polished. I have spent a full week on doing nothing but gain twist fluting a handle in ivory and working about 10 hours each day. It does take awhile and lots of asprins.
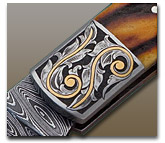
Engraving
Engraving enhances the value of anything. Knives with engraving change functional work into small art objects that are sharp. Regardless of whether it is in the field or for your collection, you will be proud that you've decided to have your work engraved. I do all of my own engraving and gold/silver work by hand, as I believe in giving you the best work that I can do.
|